Thermoforming Process Ultimate Guide 2019 With Cost - RPM Design and Prototype
Design & Build Services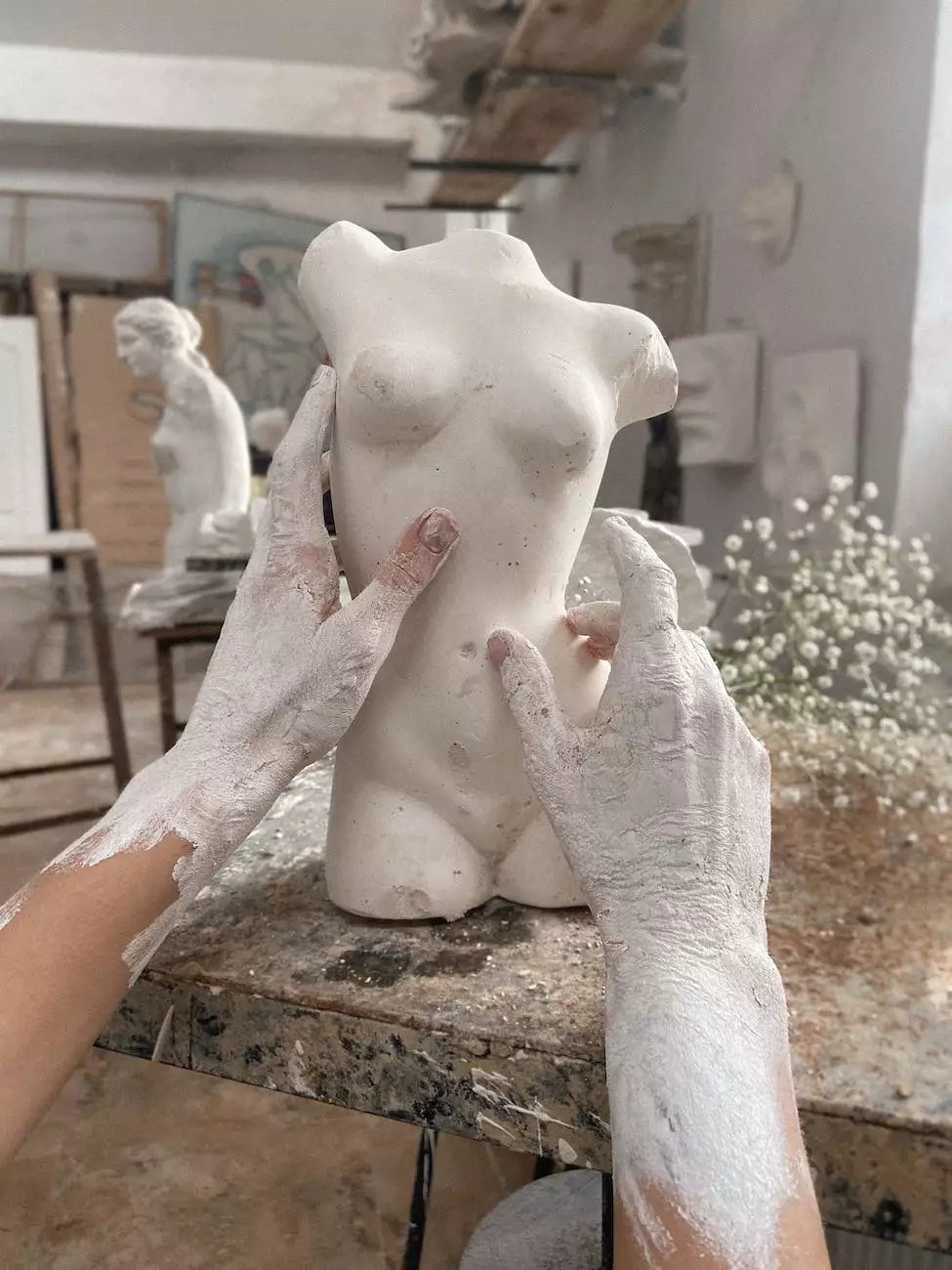
Introduction to Thermoforming
Welcome to RPM Design and Prototype's comprehensive guide on the Thermoforming process. As industry experts, we understand the importance of having detailed knowledge about thermoforming technology. In this guide, we will delve into the intricacies of the process, providing you with valuable insights and cost considerations to help you make informed decisions for your projects.
What is Thermoforming?
Thermoforming is a versatile manufacturing technique used to create plastic parts. It involves heating a plastic sheet and shaping it using molds or vacuum forming. This process is widely used due to its efficiency, cost-effectiveness, and ability to produce complex shapes with varying thicknesses.
The Thermoforming Process
The thermoforming process consists of several key steps. These include:
- Design and Prototyping: Before initiating the thermoforming process, it is crucial to develop a precise design. RPM Design and Prototype offers CAD modeling services to assist you in creating accurate prototypes for efficient product development.
- Material Selection: Selecting the right material is essential for the success of your thermoformed parts. Factors such as durability, strength, and appearance should be considered. Our team at RPM Design and Prototype will guide you in choosing the most suitable material for your specific requirements.
- Heating the Plastic Sheet: The plastic sheet, often made of materials like ABS, PVC, or polycarbonate, is heated until it becomes pliable. The precise temperature depends on the material being used.
- Forming: Once the plastic sheet reaches the appropriate temperature, it is placed over or inside the mold. Depending on the desired outcome, the sheet is either vacuum formed or pressure formed, enabling it to take the shape of the mold.
- Trimming and Finishing: After the formed plastic part has cooled and solidified, it is trimmed to remove excess material. Secondary processes such as machining, painting, or printing can also be applied to achieve the desired finish.
- Inspection and Quality Control: At RPM Design and Prototype, we prioritize quality assurance. All thermoformed parts undergo rigorous inspection to ensure they meet the highest standards before reaching our clients.
Advantages of Thermoforming
Thermoforming offers numerous advantages that contribute to its popularity in various industries. Some key advantages include:
- Cost-effectiveness: Thermoforming is a cost-effective manufacturing method, especially for large-scale production. The tooling costs are considerably lower compared to other processes like injection molding.
- Versatility: Thermoforming allows for the creation of complex shapes and designs. It can accommodate undercuts, textures, and various surface finishes, making it an ideal choice for diverse applications.
- Rapid Prototyping: With its quick setup and production time, thermoforming enables rapid prototyping. This accelerates the product development cycle and reduces time-to-market.
- Customization: Thermoforming provides flexibility in terms of color, material selection, and finishing options. It allows for customization to meet specific branding or functional requirements.
- Sustainability: Many thermoforming materials are recyclable, promoting sustainability and environmental responsibility. RPM Design and Prototype strives to use eco-friendly materials whenever possible.
Thermoforming Cost Considerations
When embarking on a thermoforming project, it is important to understand the cost implications involved. Several factors can influence the overall cost, including:
- Material Selection: The choice of material will impact the cost, as different materials have varying prices and availability. Our experts will help you select the most cost-effective option without compromising the quality and functionality of your parts.
- Tooling: The cost of tooling is a significant consideration in thermoforming. Depending on the complexity of the mold and the number of cavities required, the tooling cost can vary. Rest assured, our skilled team ensures optimal design and tooling efficiency to minimize costs while maintaining high-quality standards.
- Part Complexity and Size: The complexity and size of your thermoformed parts influence the production time and cost. Highly intricate designs or larger parts may require additional processing steps, resulting in higher costs. Our experienced team will evaluate your project and provide accurate cost estimates.
- Production Volume: The volume of parts required affects the overall cost. Thermoforming is ideal for both short and long production runs, and economies of scale can significantly lower costs for larger quantities.
- Finishing Options: Additional finishing processes, such as painting, texturing, or assembly, may be necessary depending on your project's requirements. These processes can add to the overall cost but can also enhance the aesthetics and functionality of the final product.
Applications of Thermoforming
The versatility of thermoforming makes it suitable for a wide range of applications across various industries, including:
- Automotive: Thermoformed parts are commonly used in automotive interiors, exterior panels, and even under-the-hood components.
- Medical: Medical devices, equipment enclosures, and disposable products often utilize thermoformed parts due to their cleanliness, sterility, and durability.
- Packaging: Thermoforming is extensively used in packaging applications, including blister packs, clamshells, trays, and containers.
- Aerospace: The lightweight nature and design flexibility of thermoformed parts make them ideal for aerospace applications, such as interior panels and cabin components.
- Point-of-Purchase Displays: Thermoforming offers visually appealing and structurally sound solutions for point-of-purchase displays, enhancing product visibility and marketing impact.
- Consumer Goods: Numerous consumer products, ranging from electronic enclosures to household appliances, utilize thermoformed parts for their excellent aesthetics and functionality.
Choose RPM Design and Prototype for Your Thermoforming Needs
As industry-leading experts in thermoforming, RPM Design and Prototype is dedicated to delivering high-quality, cost-effective solutions for your projects. With our extensive experience, state-of-the-art facilities, and commitment to customer satisfaction, we have earned the trust of clients across various industries.
Contact RPM Design and Prototype today to discuss your thermoforming requirements and experience the difference that our expertise can make in your next project. Reach out to us and let's create innovative solutions together.