Investment Mold Casting Process for Metal Fabricators
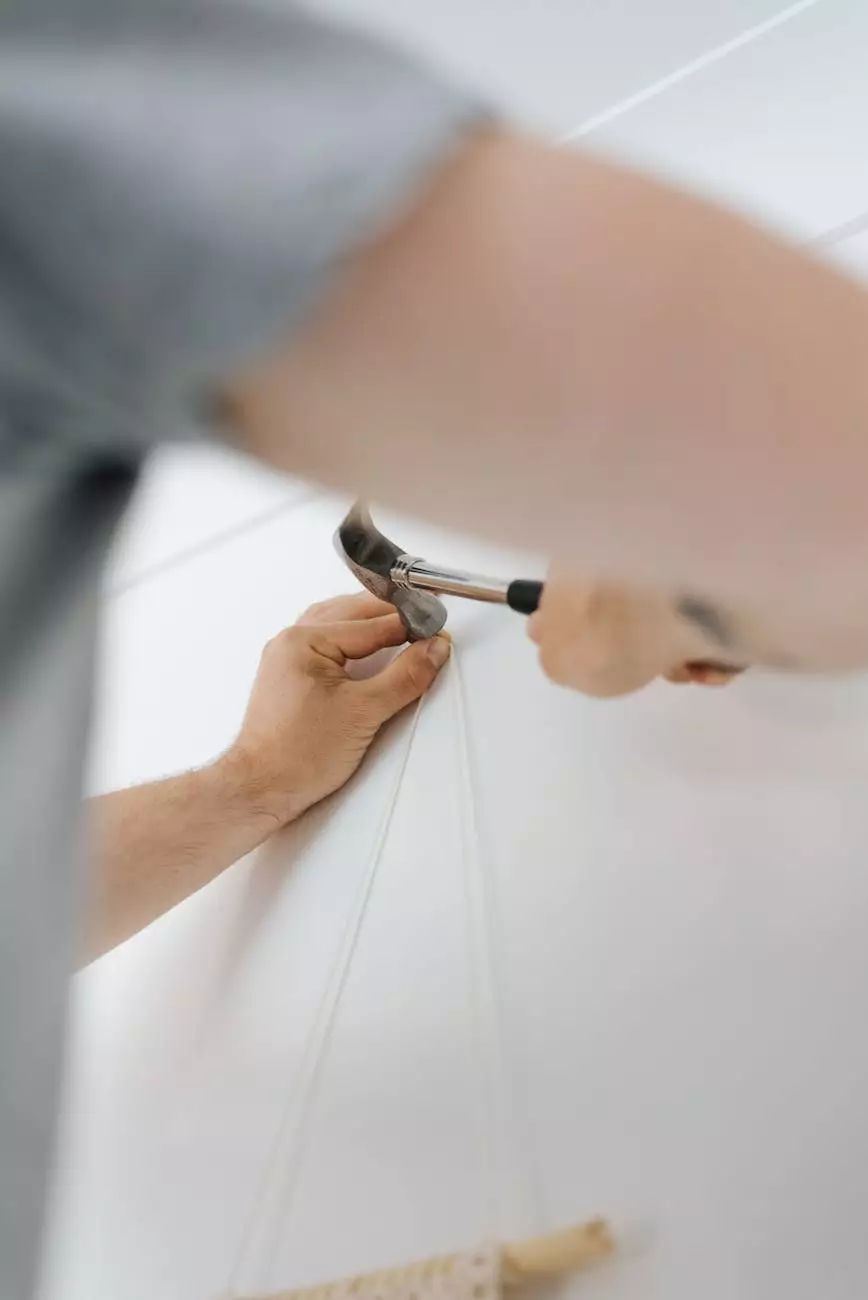
Introduction
Welcome to QuickParts.com, your go-to resource for metal fabrication services and expertise. In this article, we will delve into the investment mold casting process and explore its benefits for metal fabricators. Additionally, we will discuss the impact of 3D printing on modern manufacturing and how it complements traditional fabrication methods.
The Investment Mold Casting Process
Metal fabricators, like those at QuickParts.com, employ various techniques to meet the precise requirements of their customers. One such technique is the investment mold casting process, which allows for the production of highly intricate and complex metal parts with exceptional precision and quality.
The investment mold casting process begins with the creation of a master pattern, typically made from wax or a similar material. This pattern is used to create a mold around it, which will later be filled with molten metal. Multiple patterns can be incorporated into a single mold, enabling the production of numerous parts simultaneously.
Once the mold is created, it undergoes a process known as dewaxing, where the wax pattern is removed, leaving a cavity ready for metal infusion. Next, molten metal is poured into the cavity, filling the space previously occupied by the wax model. The metal is allowed to cool and solidify, taking the shape of the desired part.
Investment mold casting offers several advantages over other fabrication methods. First and foremost, it allows for the production of highly complex and detailed parts with exceptional surface finishes. The precision of investment mold casting ensures that the final product meets even the most stringent specifications.
The Benefits of Investment Mold Casting
Investment mold casting provides metal fabricators with numerous benefits:
- Design Flexibility: The investment mold casting process allows for intricate and complex geometries, giving metal fabricators increased design freedom. This flexibility enables the creation of unique and innovative parts that meet the specific needs of customers.
- High Accuracy and Precision: With investment mold casting, metal fabricators can achieve tight tolerances and dimensional accuracy. The process ensures repeatability, minimizing inconsistencies and defects in the final product.
- Superior Surface Finish: Investment mold casting produces parts with exceptional surface quality, reducing the need for additional finishing processes. This results in time and cost savings for metal fabricators.
- Wide Material Selection: Metal fabricators can utilize a variety of materials in the investment mold casting process, including stainless steel, aluminum, bronze, and more. This versatility allows for the production of parts with diverse mechanical properties and characteristics.
- Cost-Effective Production: Investment mold casting enables metal fabricators to produce high-quality parts in large quantities efficiently. The process minimizes material waste, lowers tooling costs, and reduces overall production time, resulting in cost savings for both fabricators and customers.
3D Printing and its Impact on Modern Manufacturing
While investment mold casting has long been a favored method among metal fabricators, the advent of 3D printing has revolutionized the manufacturing landscape. Additive manufacturing, commonly known as 3D printing, complements traditional fabrication methods and offers unique advantages in terms of rapid prototyping, design iteration, and production efficiency.
3D printing allows metal fabricators to transform digital designs into physical objects without the need for traditional tooling or molds. This technology builds objects layer by layer, using materials such as metal powders or polymers. It enables the creation of complex geometries, internal features, and lightweight structures that would be challenging or impossible to achieve with traditional manufacturing processes alone.
By leveraging 3D printing in conjunction with the investment mold casting process, metal fabricators can optimize their production workflows. 3D printing allows for the rapid production of intricate patterns and prototypes, reducing the time required for design validation and tooling preparation. This streamlines the overall manufacturing process, resulting in shorter lead times and increased productivity.
In addition to rapid prototyping, 3D printing also plays a significant role in serial production. Metal fabricators can utilize 3D-printed tooling and molds to create investment casting patterns, enhancing the efficiency and precision of the investment mold casting process. This integration of additive manufacturing and traditional fabrication methods drives innovation and enables metal fabricators to produce complex parts with enhanced performance and reduced costs.
Conclusion
The investment mold casting process remains a cornerstone of metal fabrication, providing fabricators with unparalleled design flexibility, accuracy, and surface finish. The advent of 3D printing has further complemented traditional fabrication methods, offering rapid prototyping and streamlined production workflows.
At QuickParts.com, we specialize in delivering high-quality metal fabrication services that leverage the investment mold casting process and combine it effectively with 3D printing technologies. Whether you require intricate metal parts or custom prototypes, our team of skilled professionals is dedicated to meeting your specific needs. Contact us today to learn more about our services or to discuss your project requirements!