OEM Lathe Machining Parts Factory: Driving Precision and Quality in Metal Fabrication
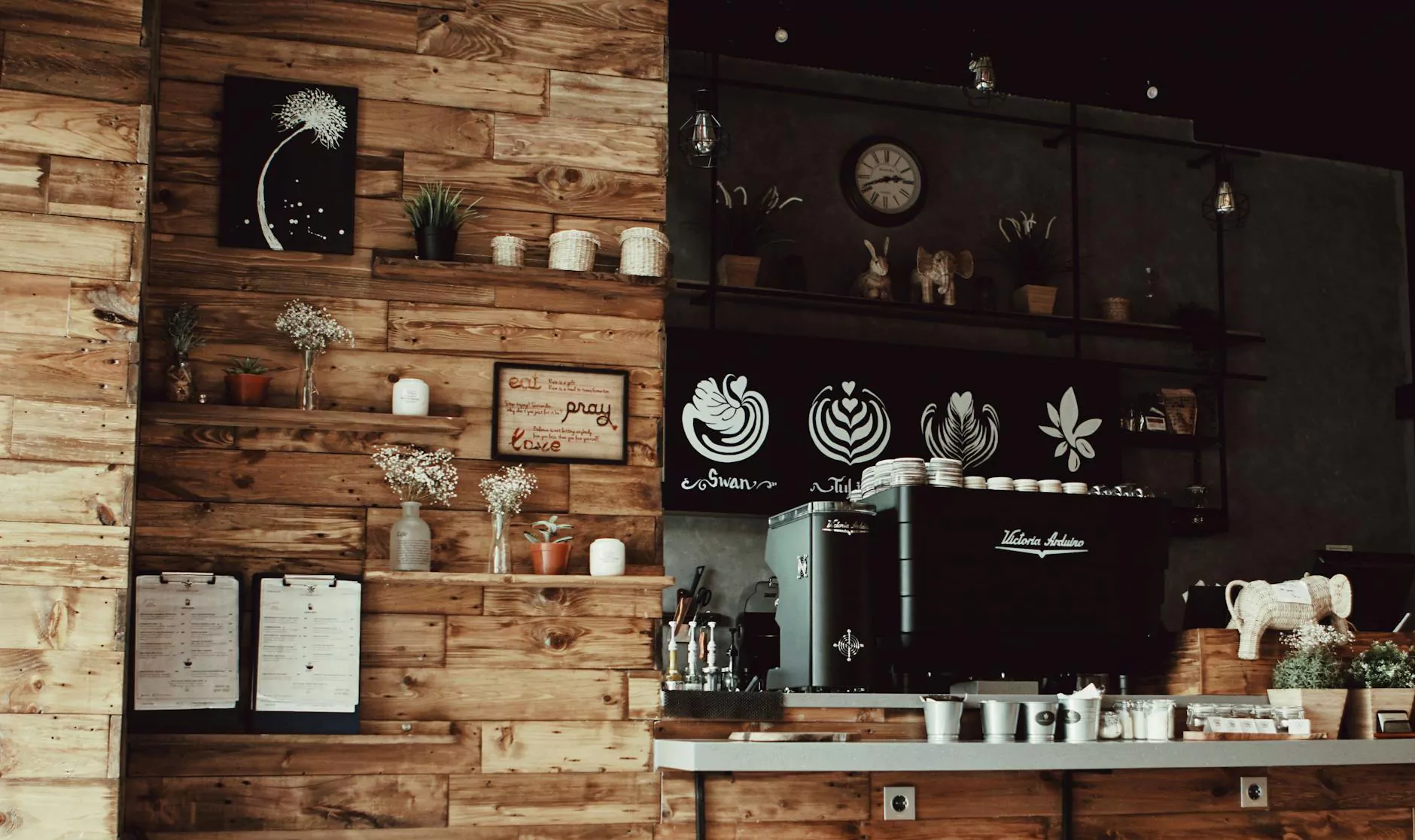
The demand for precision engineered components in various industries continues to surge as businesses strive for efficiency and quality. Among the critical contributors to this sector are OEM lathe machining parts factories, which play an indispensable role in the production of meticulously crafted parts. This article delves into the essential aspects of OEM lathe machining, emphasizing its significance, benefits, technical insights, and future trends.
Understanding OEM Lathe Machining Parts
OEM stands for Original Equipment Manufacturer, and lathe machining refers to the process of cutting, shaping, and finishing materials to create precision parts using a lathe. Lathe machining is a foundational technique in the realm of manufacturing, where cylindrical materials are rotated against cutting tools to achieve exact specifications.
What Sets OEM Lathe Machining Apart?
Partnering with an OEM lathe machining parts factory provides several distinct advantages:
- Customization: OEMs can design and manufacture parts tailored to specific customer needs, enhancing product performance.
- Scalability: These factories can scale production quickly to meet increased demands without sacrificing quality.
- Quality Assurance: Rigorous quality control processes ensure that each part meets the desired specifications and industry standards.
- Innovation: Advanced technologies and continuous improvement strategies keep OEMs at the forefront of manufacturing capabilities.
The Importance of Precision in Manufacturing
In industries such as automotive, aerospace, and medical devices, precision is not just a luxury; it is a necessity. Components must fit together perfectly and function reliably under extreme conditions. An OEM lathe machining parts factory employs state-of-the-art technology and skilled machinists to achieve this precision. Some key aspects of precision in machining include:
1. Tolerance Levels
Tolerance refers to the permissible limit of variation in a physical dimension. OEM lathe machining factories often achieve tolerances as tight as ±0.001 inches, which is critical in performance applications.
2. Materials Used
The choice of material greatly influences the performance and durability of machined parts. High-quality materials such as stainless steel, aluminum, and titanium are commonly used, each offering different benefits:
- Stainless Steel: Excellent corrosion resistance and strength.
- Aluminum: Lightweight and easily machinable, making it perfect for applications that require a reduction in weight.
- Titanium: Exceptional strength-to-weight ratio and unrivaled corrosion resistance, ideal for aerospace applications.
3. Advanced Manufacturing Technologies
Incorporating CNC (Computer Numerical Control) technology has revolutionized the lathe machining process. CNC lathes offer greater precision, automation, and repeatability, leading to enhanced productivity and reduced human error.
The Machining Process: Step by Step
Understanding the typical workflow in an OEM lathe machining parts factory provides valuable insights into the efficiency and detail involved. Here’s a breakdown of the machining process:
1. Design and Prototyping
The first step involves creating detailed designs and prototypes. Utilizing CAD (Computer-Aided Design) software allows engineers to develop intricate designs that are both functional and manufacturable.
2. Material Selection
After finalizing the design, suitable materials are chosen based on the application requirements, performance expectations, and manufacturing capabilities.
3. Machining Setup
In this phase, the selected material is secured on the lathe. Tooling is prepared, and machines are calibrated according to the design specifications.
4. Machining Operations
As the lathe rotates the material, cutting tools are employed to achieve the desired shape and finish. This can involve various operations such as turning, drilling, and threading.
5. Quality Control
Throughout the machining process, quality control measures are implemented. This may involve inspections using high-precision measuring instruments to verify that parts meet exact specifications.
6. Surface Finishing
A final check for surface finish can include treatments like anodizing, powder coating, or polishing to enhance aesthetic appeal and corrosion resistance.
Industry Applications of OEM Lathe Machining Parts
The versatility of OEM lathe machining parts extends to various sectors:
1. Automotive Industry
In automotive manufacturing, parts such as shafts, gears, and housings are produced with utmost precision to ensure optimal performance and safety. OEM parts are continuously developed to enhance vehicle efficiency and comply with regulatory standards.
2. Aerospace Sector
The aerospace industry requires components that can withstand extreme temperatures and pressures. OEM lathe machining plays a vital role in manufacturing parts such as turbine blades, landing gear components, and many more, adhering to stringent regulations.
3. Medical Devices
In the medical field, reliability is paramount. OEM lathe machining factories produce critical components for surgical instruments, implants, and diagnostic equipment, where precision can directly affect patient outcomes.
Benefits of Choosing an OEM Lathe Machining Parts Factory
Opting to work with an OEM lathe machining parts factory provides significant advantages for businesses across sectors. Here are the primary benefits:
- Expertise: OEMs specialize in specific industries, allowing them to offer unparalleled expertise and guidance throughout the production process.
- Cost Efficiency: Streamlined production processes and bulk material purchasing typically result in lower costs for manufacturers and their clients.
- Time Savings: With established systems in place, OEMs can expedite the manufacturing process, significantly reducing lead times.
- Flexibility: OEM factories often provide flexibility in production runs, catering to both small-scale and large-scale orders.
Future Trends in OEM Lathe Machining
The landscape of OEM lathe machining is continually evolving. Here are some trends that are shaping the future of the industry:
1. Automation and Robotics
The increasing integration of automation and robotics in manufacturing processes optimizes efficiency and precision, allowing for 24/7 operation without breaks.
2. Sustainable Manufacturing Practices
As sustainability becomes a key focus, OEM lathe machining factories are adopting eco-friendly practices, such as recycling materials and reducing waste during production.
3. Advanced Materials
Research into advanced materials, such as composites and smart materials, is paving the way for innovative parts that offer enhanced performance and durability.
4. Industry 4.0
The implementation of Industry 4.0 principles, which encompass IoT (Internet of Things), AI (Artificial Intelligence), and big data analytics, is revolutionizing the production processes, enabling better decision-making and enhanced production capabilities.
Conclusion: Elevating Your Manufacturing with OEM Lathe Machining Parts
For businesses seeking to enhance their manufacturing processes, incorporating components from an OEM lathe machining parts factory can be a game-changer. With the ability to offer customization, precision, and innovation, these factories are well-equipped to meet the evolving demands of diverse industries. As technology advances and industry practices shift toward greater sustainability and efficiency, those who embrace OEM lathe machining will likely find themselves at the forefront of excellence in manufacturing.
Partnering with an established OEM lathe machining parts factory, such as deepmould.net, ensures access to top-tier expertise, superior product quality, and the strategic advantage of being able to meet market demands efficiently. Embrace the future of manufacturing and elevate your capabilities with cutting-edge lathe machining solutions today!