Molding Precision in Metal Fabrication: Elevating Business Standards
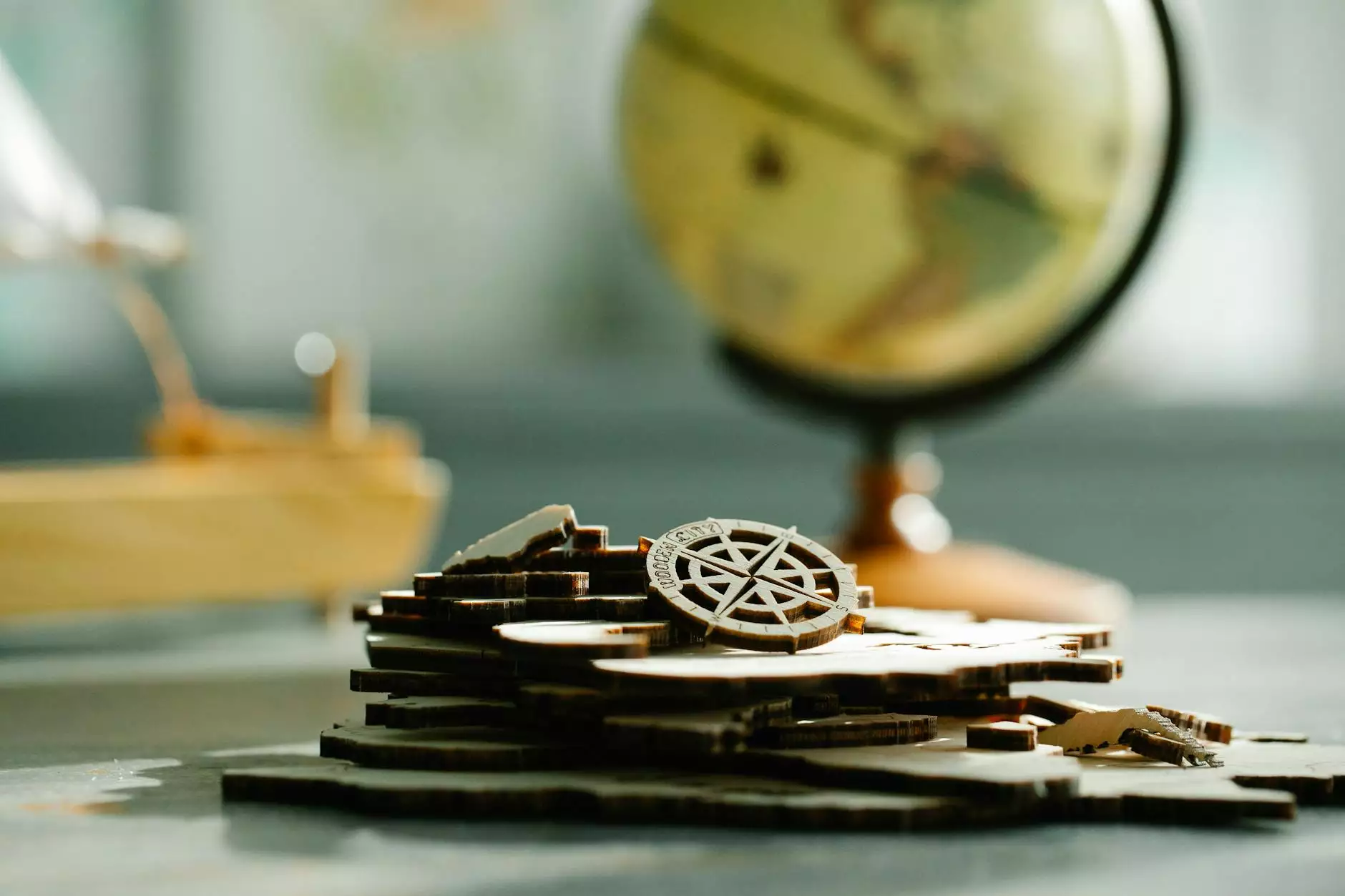
The Importance of Molding Precision in Today’s Manufacturing Landscape
Molding precision is a pivotal component in the realm of metal fabrication. In an industry that pivots on accuracy and efficiency, the ability to mold components with exact specifications can significantly impact both the production process and the final product quality. As we delve deeper into this topic, we will uncover the multifaceted advantages that molding precision brings to businesses, especially in the context of metal fabrication.
Understanding Molding Precision: A Comprehensive Overview
At its core, molding precision refers to the meticulous process of shaping materials to extremely tight tolerances, ensuring that every component fits perfectly within larger assemblies. This is particularly crucial in industries where even the slightest misalignment can lead to catastrophic failures, such as aerospace, automotive, and medical devices.
Key Aspects of Molding Precision
- Accuracy: Achieving precise dimensions and shapes.
- Consistency: Ensuring uniformity across all produced parts.
- Durability: Creating components that withstand operational stresses.
- Material Optimization: Effectively using materials to minimize waste.
How DeepMould.net Exemplifies Molding Precision
One company that stands out in the field of molding precision is DeepMould.net. With a commitment to quality and innovation, DeepMould has established itself as a leader in metal fabrication. Their expertise in molding precision not only enhances product reliability but also drives down costs through efficient production processes.
Technological Innovations in Molding
DeepMould utilizes cutting-edge technologies that facilitate high-precision molding. Some of these technologies include:
- Computer Numerical Control (CNC) Machining: This method allows for unparalleled precision in shaping metal components.
- Advanced Molding Techniques: Techniques such as injection molding and die casting are adapted to achieve high levels of accuracy.
- Quality Control Systems: Rigorous inspection routines ensure that every piece produced meets the high standards set by the industry.
Benefits of Molding Precision in Metal Fabrication
The implications of molding precision extend beyond mere aesthetics. Let's explore some of the crucial benefits that businesses can gain from leveraging precise molding practices:
1. Enhanced Product Performance
In industries such as aerospace and automotive, where performance is paramount, molding precision directly correlates with how parts perform under stress. Well-molded components have reduced wear and tear, leading to longer lifespans and reduced maintenance costs.
2. Increased Efficiency
Precision in molding reduces the need for reworks and adjustments. This efficiency translates into faster production times, allowing businesses to meet tight deadlines without compromising on quality. Companies like DeepMould.net exemplify this ethos by streamlining their manufacturing processes to enhance output.
3. Cost Reduction
While it may seem counterintuitive, investing in molding precision can lead to overall cost savings. By minimizing waste and optimizing material use, businesses can significantly reduce their operational expenses. Additionally, high-quality components result in lower warranty claims and customer returns.
4. Competitive Advantage
In a crowded marketplace, having the ability to deliver high-precision parts can set a business apart. Companies known for their quality attract more clients and build stronger brand loyalty. DeepMould.net has leveraged its precision molding capabilities to become a trusted partner for many businesses across sectors.
Challenges in Achieving Molding Precision
While the benefits of molding precision are manifold, reaching that level of precision comes with its challenges. Here are some common issues faced in the pursuit of high-quality molding:
1. Material Variability
The characteristics of the raw materials used can vary, affecting the precision of the molding process. Businesses need to work closely with suppliers to select high-quality materials that minimize variability.
2. Equipment Limitations
Not all fabrication equipment is created equal. Outdated machines may not provide the necessary precision. Investing in modern machinery is essential for maintaining high standards of molding precision.
3. Skilled Workforce
Achieving top-tier molding precision requires an experienced workforce that understands the nuances of the molding process. Continuous training and skill development are crucial in maintaining high quality.
The Future of Molding Precision in Metal Fabrication
The landscape of metal fabrication is always evolving. With advancements in technology and increasing demand for high-quality products, molding precision is likely to remain a critical area of focus for manufacturers. Future trends may include:
1. Automated Manufacturing Processes
Automation will play a significant role in enhancing precision. Robotic systems can perform repeatable tasks with exceptional accuracy, reducing human error.
2. 3D Printing Innovations
The rise of 3D printing technology in metal fabrication also points to a new era of molding precision. The ability to create highly customized parts on demand will revolutionize the industry.
3. Sustainable Practices
As businesses become more environmentally conscious, the focus on sustainability will influence molding practices. Adaptive techniques that minimize waste while maintaining precision will become essential.
Conclusion
In summary, molding precision isn't just a technical requirement but a cornerstone of successful metal fabrication. Companies like DeepMould.net are setting benchmarks by integrating advanced technologies and practices that enhance quality, reduce costs, and improve efficiency. By embracing the principles of precision molding, businesses can not only meet the demands of their industries but also excel in delivering unparalleled value to their customers. The future of metal fabrication is bright, with the promise of greater innovations and standards in molding precision anticipated to shape the next generation of manufacturing.