The Power of Digital Light Processing Technology in Metal Fabrication and 3D Printing
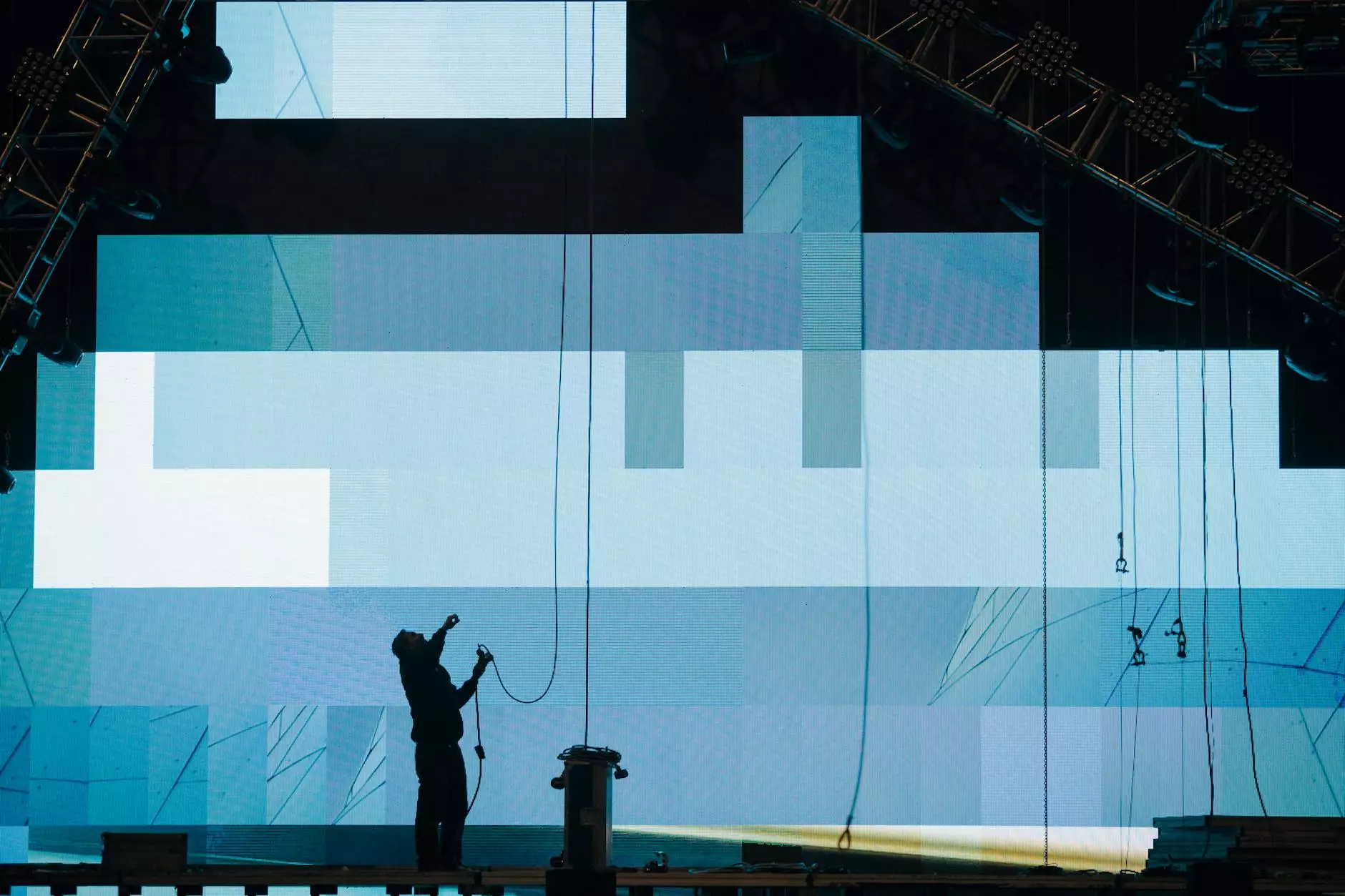
Introduction
In this digital era, technological advancements have revolutionized various industries. One such innovation that has reshaped the landscape of metal fabrication and 3D printing is Digital Light Processing (DLP) technology. Quick Parts, a renowned name in the field of Metal Fabricators and 3D Printing, has been at the forefront, harnessing the immense potential of DLP technology to enhance their operations and deliver exceptional results for their clients.
What is Digital Light Processing Technology?
Digital Light Processing (DLP) is a cutting-edge additive manufacturing technique that utilizes digital micromirror devices (DMDs) to create high-resolution and precise three-dimensional objects. Unlike traditional manufacturing processes, DLP technology involves selectively curing liquid resin layer by layer using UV light. This enables the creation of complex geometries with outstanding accuracy and speeds up the manufacturing process significantly.
Metal Fabrication with DLP Technology
Quick Parts has embraced DLP technology as a vital tool in their Metal Fabrication processes. With its impressive precision and speed, DLP enables the production of intricate metal components with exceptional surface finish. The ability to manufacture complex parts in a fraction of the time traditional methods would require gives Quick Parts a competitive edge in the industry.
Whether it's custom sheet metal fabrication, CNC machining, or metal component assembly, Quick Parts leverages DLP technology to meet the diverse needs of their clients with unparalleled quality and efficiency. The use of DLP also allows for seamless integration between design and production, reducing lead times and ensuring accurate replication of intricate designs.
Advantages of DLP Technology in Metal Fabrication
DLP technology offers a multitude of advantages when it comes to metal fabrication:
- High Precision: The accuracy and precision achieved through DLP technology are unmatched, ensuring consistent quality and dimensional accuracy in the manufactured parts.
- Complex Geometries: DLP enables the creation of complex and intricate geometries that would otherwise be challenging or impossible with traditional methods.
- Fast Turnaround Times: The rapid curing process and increased build speeds minimize production time, allowing for quicker project completion and faster delivery to clients.
- Cost-Effectiveness: By reducing manual labor and material waste, DLP technology offers cost savings over traditional manufacturing methods.
- Enhanced Surface Finish: DLP ensures a smoother surface finish, eliminating the need for additional post-processing steps and delivering high-quality components.
Applications of DLP Technology in Metal Fabrication
The applications of DLP technology in Metal Fabrication are vast and diverse, ranging from aerospace and automotive industries to medical devices and jewelry production:
- Aerospace: DLP technology enables the production of lightweight and high-strength components used in aircraft and spacecraft, leading to improved fuel efficiency and performance.
- Automotive: DLP is utilized to manufacture complex engine parts, prototype vehicles, and custom-designed components, enhancing manufacturing agility and customization options.
- Medical Devices: The high precision and accuracy of DLP make it ideal for creating intricate medical devices, such as dental implants and surgical tools, ensuring optimal fit and functionality.
- Jewelry and Fashion: DLP technology allows for the production of finely-detailed jewelry pieces and fashion accessories, enabling designers to bring their creative visions to life.
3D Printing and DLP Technology
In addition to metal fabrication, Quick Parts utilizes DLP technology to deliver exceptional 3D printing solutions. With its ability to produce intricate and finely detailed models, DLP has become a game-changer in the world of additive manufacturing.
Quick Parts' advanced 3D printers utilize DLP technology to create highly accurate prototypes, functional models, and end-use parts. From concept validation to functional testing, DLP-based 3D printing offers unmatched accuracy, intricate details, and excellent surface quality.
Advantages of DLP Technology in 3D Printing
The advantages of using DLP technology in 3D printing are numerous:
- Exceptional Precision: DLP ensures precise layer-by-layer curing, resulting in highly detailed 3D printed objects with fine features and textures.
- Wide Material Compatibility: DLP technology supports a variety of materials, including photopolymer resins with different properties, allowing for versatility in 3D printing applications.
- Fast Print Speed: DLP printers can achieve significantly faster printing speeds compared to other 3D printing technologies, enabling swift project completion.
- Smooth Surface Finish: DLP technology produces parts with a smooth surface finish, reducing the need for post-processing and delivering exceptional visual appeal.
- Functional Prototypes: With the ability to accurately replicate complex geometries, DLP technology facilitates the creation of functional prototypes for testing and evaluation.
Applications of DLP Technology in 3D Printing
DLP technology finds wide-ranging applications in the field of 3D printing:
- Product Design and Development: DLP allows designers and engineers to rapidly iterate and refine product designs, expediting the development process.
- Dentistry and Orthodontics: DLP-based 3D printing is employed for producing dental models, aligners, crowns, and other dental appliances, ensuring precision and patient comfort.
- Art and Sculpture: Artists and sculptors utilize DLP technology to create intricate and detailed art pieces, pushing creative boundaries and opening new possibilities.
- Education and Research: DLP-based 3D printers are valuable tools in educational institutions and research facilities, fostering innovation and hands-on learning.
Conclusion
Quick Parts, as a leading Metal Fabricators and 3D Printing company, has harnessed the power of Digital Light Processing (DLP) technology to excel in their field. Through its precise and rapid additive manufacturing capabilities, DLP technology allows for the production of highly complex metal components with exceptional surface finish. Furthermore, in the realm of 3D printing, DLP technology has revolutionized the industry with its ability to create detailed and functional objects.
DLP technology's advantages extend beyond Metal Fabrication and 3D Printing, finding applications in various sectors, including aerospace, automotive, medical, and fashion. With its continuous focus on innovation and leveraging cutting-edge technologies, Quick Parts remains at the forefront of the industry, delivering exceptional results to its clients.
Embracing Digital Light Processing technology in both Metal Fabrication and 3D Printing can provide businesses with a competitive edge, enabling them to meet evolving customer demands, accelerate project timelines, and achieve remarkable outcomes. Quick Parts stands as a testament to the success that can be achieved by integrating this groundbreaking technology into business operations.