Rubber Compression Molding Process 2019 Ultimate Guide
Blog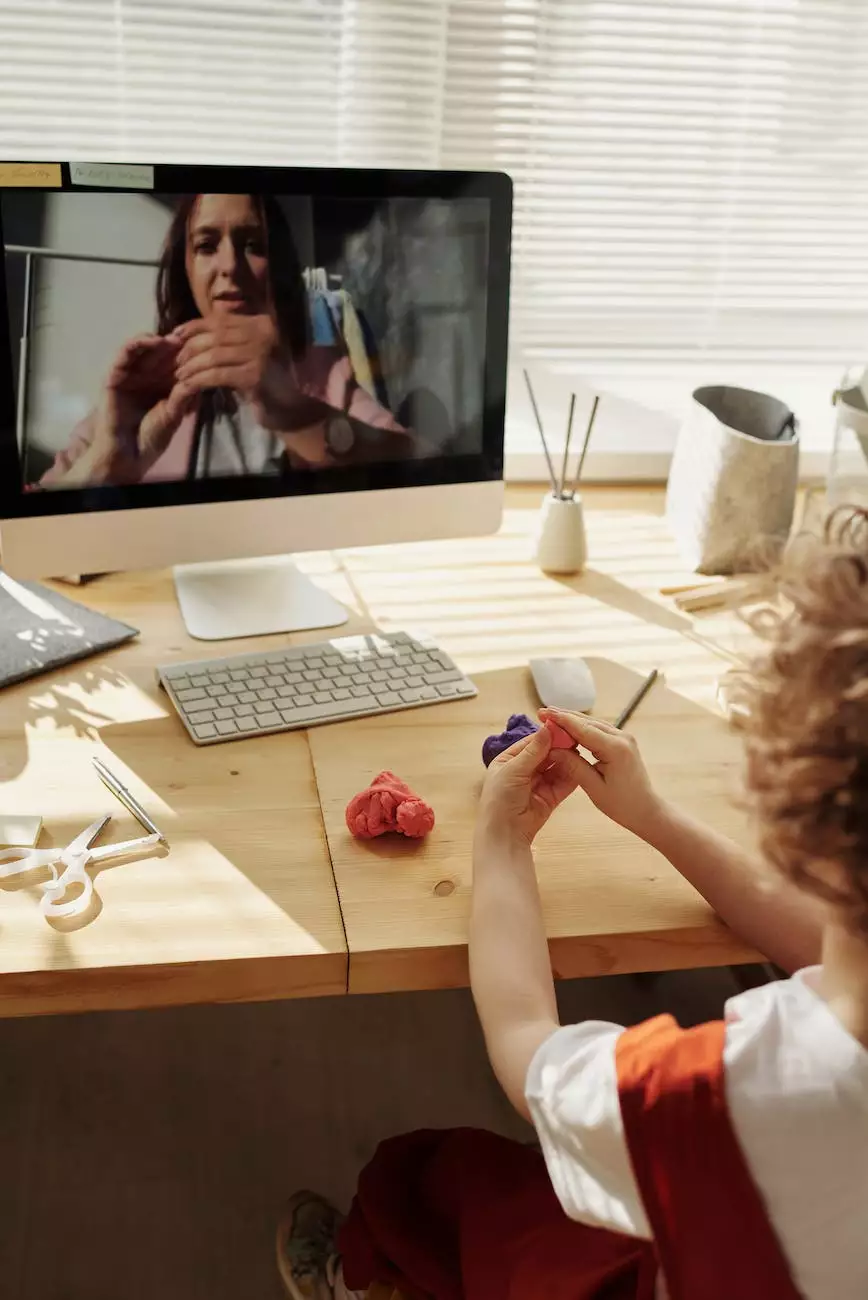
Introduction
Welcome to RPM Design and Prototype's ultimate guide to the rubber compression molding process. In this comprehensive guide, we will take a deep dive into the manufacturing techniques, materials, advantages, and much more related to rubber compression molding in 2019.
Chapter 1: Understanding Rubber Compression Molding
Rubber compression molding is a highly efficient and widely used manufacturing process for producing various rubber components. It involves the use of a compression mold, heat, and pressure to shape and cure rubber materials. This process is known for its versatility and ability to create complex and precise parts.
1.1 The Basic Process Steps
The rubber compression molding process typically includes the following steps:
- Preparation of raw materials
- Preheating the mold and rubber materials
- Load the preheated rubber material into the mold cavity
- Apply high pressure to the mold for a specific period
- Cooling and demolding
- Finishing and post-processing
This step-by-step approach ensures that the rubber material is properly shaped, cured, and ready for use.
1.2 Advantages of Rubber Compression Molding
Rubber compression molding offers several advantages over other manufacturing processes. Some key benefits include:
- Flexibility in design and shape complexity
- Cost-effectiveness for low to medium production volumes
- Ability to use various rubber materials, including silicone, EPDM, and more
- High precision and tight tolerances
- Excellent part consistency and quality
- Suitability for both simple and complex geometries
These advantages make rubber compression molding a preferred choice for many industries, including automotive, aerospace, medical, and more.
Chapter 2: Materials Used in Rubber Compression Molding
One of the critical factors in the success of the rubber compression molding process is the selection of appropriate materials. Various rubber materials are used based on specific requirements, such as:
2.1 Silicone Rubber
Silicone rubber is widely used in applications requiring resistance to extreme temperatures, weathering, and chemicals. It offers excellent flexibility, durability, and electrical insulating properties.
2.2 EPDM Rubber
EPDM rubber is highly versatile and offers excellent resistance to aging, UV exposure, and harsh weather conditions. It is commonly used in automotive seals, electrical insulation, and other industrial applications.
2.3 Natural Rubber
Natural rubber is derived from the sap of rubber trees and is known for its high elasticity and resilience. It is used in various applications ranging from tires to industrial components.
Chapter 3: The Tooling and Equipment
Accurate tooling and equipment are crucial for the successful execution of the rubber compression molding process. RPM Design and Prototype ensures the highest quality tooling and equipment, including:
3.1 Mold Design and Fabrication
Our experienced team designs and fabricates molds tailored to meet specific customer requirements. We utilize advanced software and CNC machining to ensure precision and efficiency.
3.2 Hydraulic and Mechanical Presses
RPM Design and Prototype utilizes state-of-the-art hydraulic and mechanical presses for the compression molding process. These machines provide the necessary force and control for consistent and high-quality parts.
Chapter 4: Quality Assurance and Inspection
Quality assurance is a top priority at RPM Design and Prototype. We adhere to stringent quality control procedures to ensure that each rubber component meets the highest standards. Our quality assurance process includes:
4.1 Material Testing and Verification
Before production, all raw materials undergo thorough testing and verification to confirm their quality and consistency.
4.2 Dimensional Inspection
We utilize advanced measuring equipment and techniques to perform precise dimensional inspection on each molded part. This ensures that the final products meet the required specifications.
4.3 Physical and Mechanical Testing
Physical and mechanical testing is conducted to assess the strength, durability, and performance characteristics of the rubber components.
Chapter 5: Applications and Industries
Rubber compression molding finds extensive applications across various industries. Some notable applications include:
5.1 Automotive Industry
The automotive industry extensively utilizes rubber compression molding for manufacturing seals, gaskets, o-rings, vibration mounts, and other critical components.
5.2 Aerospace Industry
Rubber compression molding plays a vital role in the aerospace industry for producing seals, grommets, gaskets, and other components that require high-performance materials and precision.
5.3 Medical and Pharmaceutical Industry
Medical and pharmaceutical applications utilize rubber compression molding for producing medical-grade components, such as diaphragms, seals, and connectors that require strict adherence to quality standards.
Conclusion
In conclusion, RPM Design and Prototype's ultimate guide to the rubber compression molding process provides comprehensive insights into this versatile manufacturing technique. With our expertise, high-end equipment, and commitment to quality, we deliver reliable and high-performance rubber components for various industries. Contact us today to learn more about our manufacturing capabilities and discuss your specific requirements.