Roll Forming Process | Ultimate Guide 2020
Machine Tooling Design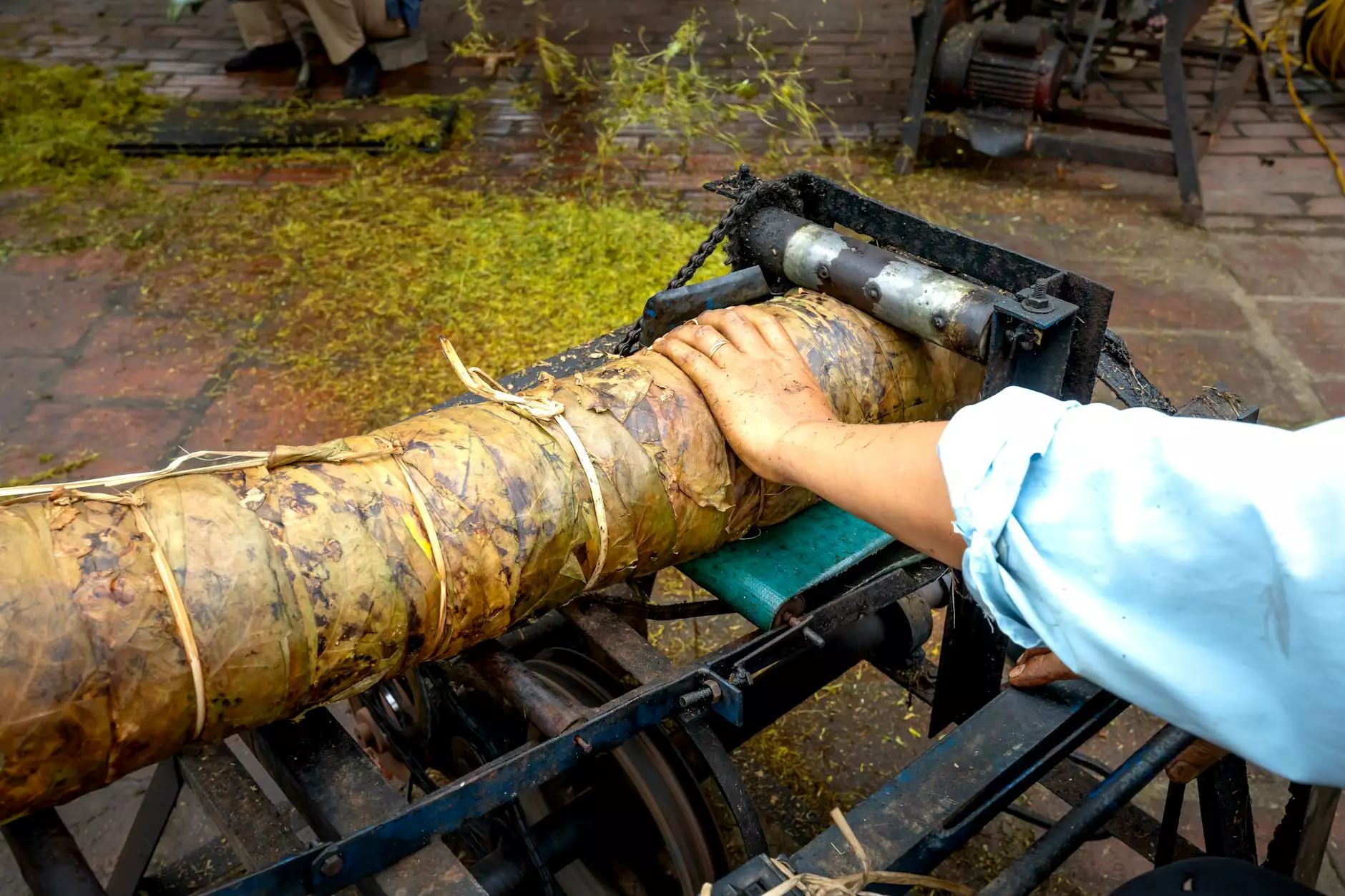
The Basics of Roll Forming
Roll forming is a highly efficient metal forming process used in various industries, including automotive, construction, and manufacturing. At RPM Design and Prototype, we specialize in providing cutting-edge roll forming solutions to meet the diverse needs of our clients.
Understanding the Roll Forming Technique
The roll forming process involves feeding a continuous strip of metal through a series of rolls, gradually shaping it into the desired profile. This technique offers numerous advantages, such as high production rates, cost-effectiveness, and the ability to produce complex cross-sections with tight tolerances.
The Roll Forming Process Steps
There are several key steps involved in the roll forming process:
- Material Selection: Choosing the right material for the desired application is crucial. Various metals, including steel, aluminum, and copper, can be used in roll forming.
- Strip Preparation: The metal strip goes through a cleaning process and may be coated or pre-painted before entering the roll forming line.
- Roll Tooling Design: Custom roll tooling is designed to achieve the desired profile shape. This step is critical for obtaining accurate and consistent results.
- Feed and Form: The prepared metal strip is fed into the roll forming machine, where a series of rolls progressively bend and shape the metal into the desired profile.
- Cutting and Shearing: Once the profile is formed, the continuous part is cut into individual lengths using flying cutoff techniques, hydraulic shearing, or other cutting methods.
- Additional Operations: Depending on the specific requirements, additional operations such as punching, slotting, embossing, or welding may be performed to further enhance the functionality of the formed part.
- Quality Control: Rigorous quality control measures ensure that the final product meets the specified standards before it is ready for distribution or assembly.
Applications of Roll Forming
Roll forming is widely employed in various industries due to its versatility and efficiency. Some common applications include:
- Automotive Industry: Roll-formed components are used in automobile frames, bumpers, wheel arches, and structural parts.
- Construction and Architecture: Roll-formed profiles find their use in roofing, wall panels, window frames, and door frames.
- Electrical Enclosures: Roll-formed enclosures provide protection and support for electrical equipment.
- Storage and Shelving: Roll-formed shelving systems are popular in warehouses, retail stores, and offices.
- Furniture and Appliances: Roll-forming techniques are applied to create components for furniture, appliances, and fixtures.
Benefits of Roll Forming
By choosing roll forming for your manufacturing needs, you can enjoy various benefits:
- Cost-Effective Production: Roll forming offers efficient and economical mass production capabilities, reducing material waste and labor costs.
- Design Flexibility: With custom roll tooling, complex and intricate profiles can be achieved, allowing for greater design possibilities.
- High Strength and Accuracy: Roll-formed parts exhibit excellent strength, dimensional accuracy, and consistency.
- Increased Productivity: The continuous nature of roll forming streamlines the production process, resulting in higher output rates.
- Material Savings: Roll forming allows for the utilization of thinner materials without compromising structural integrity, leading to material savings.
Choose RPM Design and Prototype for Your Roll Forming Needs
At RPM Design and Prototype, we are committed to delivering top-notch roll forming solutions tailored to your unique requirements. Our skilled team, state-of-the-art equipment, and dedication to quality ensure that you receive the highest level of service.
With our extensive experience in the industry, we have successfully partnered with clients from various sectors, helping them realize their visions and achieve remarkable results through the roll forming process.
Contact us today to discuss your roll forming needs and discover how RPM Design and Prototype can be your trusted partner for all your metal forming requirements.