Aluminum Extrusion Process Guide 2019: With Cost & Benefits
Design & Build Services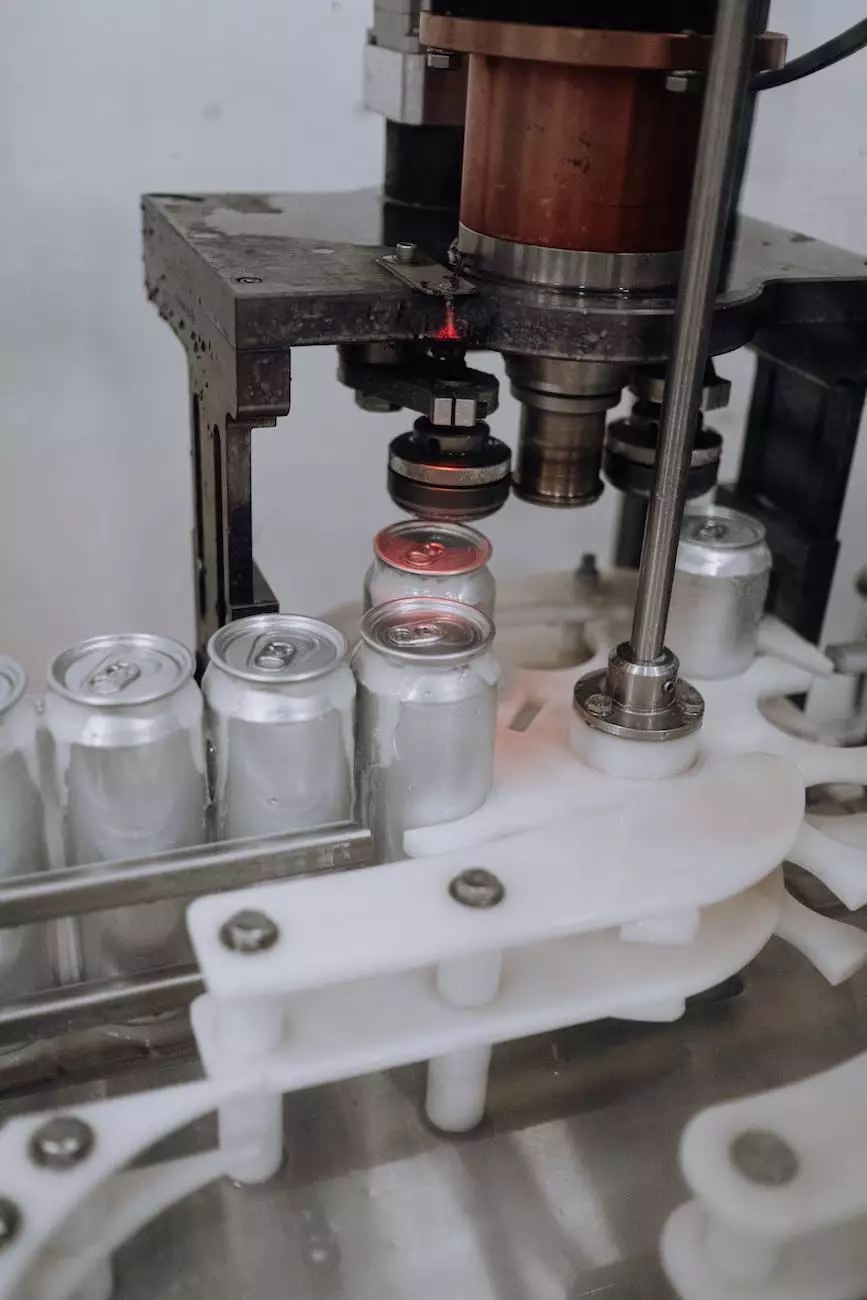
Introduction
Welcome to RPM Design and Prototype's comprehensive guide on the Aluminum Extrusion Process! If you're searching for detailed information on this versatile manufacturing method, you've come to the right place. In this guide, we will explore the aluminum extrusion process, its benefits, the associated costs, and its applications across various industries.
What is the Aluminum Extrusion Process?
The aluminum extrusion process is a widely utilized technique in which aluminum alloy billets are heated and forced through a shaped opening in a die, resulting in the creation of complex, durable profiles with uniform cross-sections. This process allows for the production of custom-designed aluminum components that meet specific requirements.
Advantages of Aluminum Extrusion
Aluminum extrusion offers numerous advantages, making it a preferred choice for many applications. First and foremost, aluminum is lightweight while maintaining excellent strength and durability. This makes it ideal for industries such as automotive, aerospace, and construction. Additionally, aluminum is corrosion-resistant, non-magnetic, and highly conductive, making it suitable for electrical and electronic applications.
The Aluminum Extrusion Process in Detail
The aluminum extrusion process starts with the design and creation of a custom die, which determines the cross-sectional shape of the final product. Once the die is ready, aluminum billets are heated to a specific temperature and loaded into an extrusion press. The press applies substantial force to push the softened aluminum through the die, resulting in the desired shape.
Step 1: Heating
Prior to extrusion, the aluminum billets are heated in a furnace to facilitate the malleability of the material. Heating is crucial to ensure successful extrusion and the desired mechanical properties of the final product.
Step 2: Die Design and Preparation
The die, often made of tool steel, is designed to accommodate the specific shape and dimensions required for the extruded profile. Precision in die design is essential to achieve accurate and uniform profiles.
Step 3: Extrusion Process
During extrusion, the heated aluminum billet is loaded into the extrusion press. The press applies tremendous force, typically ranging from 1,000 to 15,000 tons, pushing the softened aluminum through the die opening. This results in the creation of the cross-sectional shape defined by the die.
Step 4: Cooling and Aging
After the extrusion process, the newly formed profile is cooled to solidify its shape. Extruded aluminum profiles can be further subjected to a process called aging, which enhances their mechanical properties through controlled heat treatment.
Cost Considerations
The cost of aluminum extrusion depends on various factors, including the complexity of the profile, the required tolerances, surface finish, and the quantity of the final product. Custom dies, used for unique profile designs, can also affect the overall cost. However, considering the numerous advantages and long-term savings offered by aluminum extrusion, it remains a cost-effective solution for many applications.
Applications of Aluminum Extrusion
The versatility of aluminum extrusion allows for a wide range of applications across various industries. From architectural structures and automotive components to electronics enclosures and renewable energy systems, aluminum extrusion finds its place in numerous products and systems. Its flexibility, lightweight nature, and design adaptability make it an invaluable resource for designers and engineers alike.
Conclusion
In conclusion, the aluminum extrusion process offers unmatched design freedoms and numerous advantages when compared to alternative manufacturing techniques. At RPM Design and Prototype, we specialize in delivering high-quality aluminum extrusion solutions tailored to our clients' unique requirements. With our expertise and state-of-the-art facilities, we are committed to providing exceptional products that meet and exceed expectations. Contact us today to learn more about our aluminum extrusion capabilities!